DriSteem helps improve print consistency for a national leader in commercial display graphics
The Job
Modernistic is one of the nation’s leading suppliers of commercial display graphics and industrial OEM products. The company, headquartered in Stillwater, MN, was founded in 1938 as a specialty die cutter. Modernistic later added commercial screen printing, and finally, acknowledging numerous breakthroughs in digital press technology, acquired their first major digital printing press in 2004. While demand for screen printing remains high, digital press technology allows Modernistic to adapt to their customers’ changing needs — most notably speed, quality, and the variety of surfaces onto which their display graphics are printed.
In the early days of digital presses, customers willingly sacrificed image quality for quick turn-around times and lower costs. However, by 2013, ink and nozzle breakthroughs and improved media had advanced digital printing to a level where the image quality contended with screen printing.
In 2014, Modernistic acquired a digital press capable of image resolution as high as 1200 x 1200 dots per inch and fast enough to print 61 ten-foot by five-foot sheets per hour. The keys to such ultra-high resolution and speed are ink droplet size and the number of nozzles. Each of the droplets dispensed from the printer’s 42,000 nozzles has a volume of nine picoliters, which is nine trillionths of a liter. The diameter of each droplet is 5.55 microns, or 1/180th of a millimeter.
The Challenge
Some of the print jobs coming off Modernistic’s new press had unwanted smears of ink caused by static electricity. The microscopic ink droplets, having so little mass, are extremely sensitive to even the tiniest influence. Droplets pulled off
course by a static charge merge into a blob, which splashes onto the media and leaves a very visible smear. Ultraviolet light then cures the ink, including the smear, the moment it is applied. Press operator Eric Madison witnessed this phenomenon too frequently. “With too much static electricity, the reject rate can be as high as one out of every seven pieces,” he explains. “We needed a better way to control static in the shop.”
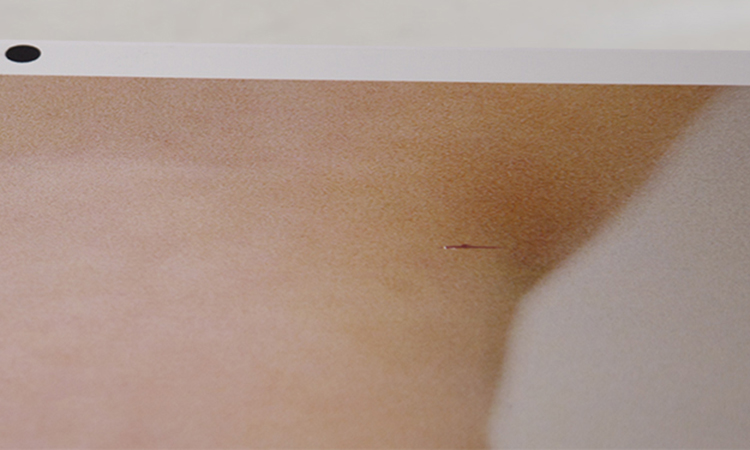
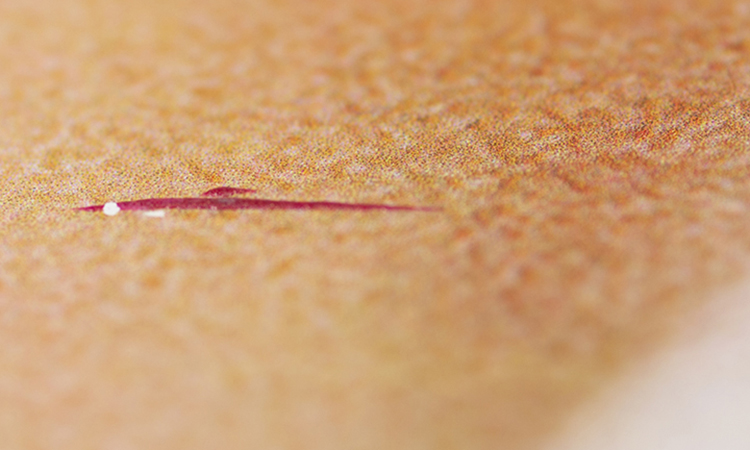
The Solution
Mark Gorski, Modernistic’s vice president of operations, knows the pitfalls of poor air quality in a print shop. Long
before new digital press went online, Gorski had implemented systems for maintaining indoor air quality throughout the plant. The building’s entire air volume was circulated several times a day through a garage-sized bank of ultra-fine filters. Air temperatures were carefully monitored and controlled in each of the four print rooms. Even the forklifts used only the cleanest-burning fuel, and a boiler as old as the 1970s building produced steam for humidification.
“But we needed a humidification system to replace the old boiler,” recalls Gorski. “A system that could humidify at a high enough volume and precisely enough for the digital press room. That’s where it had to work. Even in the winter.”
DriSteem’s high-pressure system was the perfect solution for Modernistic, because it provides high-capacity humidification along with flexibility in multiple zones, and all with a single pump station. Plus, the evaporative cooling effect offsets the building’s cooling load. DriSteem’s high-pressure system has been running at Modernistic since the fall of 2015. Asked about the reject rate on his digital press, Madison said, “It’s down to 1 in 40.”
The Results
- Lowered the reject rate for large-format digital press output from 14 percent to 2.5 percent
- Lowered the customer’s electricity consumption enough to qualify for a significant utility rebate
Notes
The dispersion grid includes 900 atomizing nozzles in 2,400 feet of tubing. In the mechanical room, water softeners and reverse osmosis water treatment systems make pure water for the High-pressure System. The system atomizes 1,200 gallons per hour for humidification and, for a summertime bonus, free cooling.
Resources
For more information on DriSteem products mentioned in this case study, go to:
DriSteem Water Treatment Systems
Start a Project
Expert Partner: A local DriSteem rep will work with your facilities team to identify the best solutions available for your application. They will review existing systems and spaces to determine the best way to reach the ideal RH range to improve processes and protect your valuable equipment, materials, and people.